Buy Now
$4,123 $4,850
15% off
$4,840 $6,050
20% off
$5,845 $8,350
30% off
Buy now
Premium Report Details
Base Year: 2024
Companies covered: 15
Tables & Figures: 34
Countries covered: 19
Pages: 138
Download Free PDF
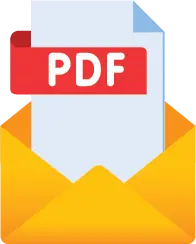
Cement Waste Heat Recovery System Market
Get a free sample of this reportGet a free sample of this report Cement Waste Heat Recovery System Market
Is your requirement urgent? Please give us your business email for a speedy delivery!
Cement Waste Heat Recovery System Market Size
The global cement waste heat recovery system market size was valued at USD 15.8 billion in 2024 and is estimated to reach the value of USD 32.6 billion by 2034, growing at a CAGR of 7.7% from 2025 to 2034. Cement plants consume a lot of energy, and waste heat recovery systems can significantly reduce this energy use. By capturing and reusing heat that would otherwise be wasted, these systems lower fuel costs and increase profits for companies.
In citation, in 2023, the Bureau of Energy Efficiency reported a successful retrofit of a waste heat recovery boiler on a cement line, resulting in a 12% reduction in thermal energy use, a savings of 78,000 gigajoules (GJ) of fuel per year, and a payback period of just 14 months at current fuel prices.
Governments are implementing stricter regulations to limit emissions, pushing cement manufacturers to lower their carbon footprints. Waste heat recovery systems help these companies meet environmental standards and grow in the market. For instance, any Portland cement plant that emits 25,000 tons of CO? equivalent per year must report its greenhouse gas emissions by July 31. In 2023, 113 U.S. facilities reported a total of 41.3 million tons of CO? equivalent emissions, leading 69% of these plants to adopt waste heat recovery systems, which helped cut about 5% of process emissions.
Tax incentives and subsidies further promote the installation of waste heat recovery systems, making it financially easier for companies to invest in clean energy technologies. This not only benefits the environment by reducing greenhouse gas emissions but also allows companies to stay competitive in the market. For instance, in 2023, the Bureau of Energy Efficiency offered financial support through the Partial Risk Guarantee Fund for Energy Efficiency, providing loans of USD 10 to 500 million at lower interest rates, promoting a 65% increase in waste heat recovery installations in the cement sector.
Advancements in heat recovery technology are also enhancing efficiency and reducing operational costs for companies, making them more attractive to environmentally conscious consumers. Modern designs are more dependable and cost-effective to support, attracting more cement producers. According to a draft report from the U.S. Department of Energy in May 2024, next-generation waste heat recovery technologies, including organic rankine cycle systems and smart controls using digital analysis, can improve energy recovery efficiency by up to 30% and reduce downtime for maintenance through predictive diagnostics.
President Trump instituted tariffs in April 2025, hence, cement waste heat recovery system market will be affected. All imports are now subject to a tax of 10% and higher rates for specific countries, the cost of necessary components, including turbines and sensors, will increase. Rising costs of steel, heat exchangers, and control systems strain manufacturers reliant on global supply chains. Companies may hike prices or delay projects, curbing market growth.
Cement Waste Heat Recovery System Market Trends
Cement plants are increasingly using waste heat recovery alongside solar and biomass energy to cut down their environmental impact and enhance energy efficiency. This shift towards combining renewable energy sources is helping cement manufacturers in sustainable practices. For instance, a recent project in Rajasthan, MNRE's Annual Report for 2023–24, successfully blended a 7 MW waste heat recovery system with a 5 MW solar power array and 3 MW of biomass energy. This setup resulted in an 18% reduction in fuel costs, saving 125,000 gigajoules of energy each year while providing consistent power around the clock.
Real-time monitoring tools are being employed to keep an eye on system performance, helping to minimize waste and downtime, and offering valuable insights for ongoing improvements. By harnessing multiple renewable energy sources, cement plants not only lower their carbon emissions but also bolster their energy stability. For instance, under the Bureau of Energy Efficiency’s latest initiative, 25 cement companies have been required to implement real-time Energy Management Systems, which have helped reduce unexpected downtime by 6% and waste heat loss by 4% in 2023.
Developing countries are increasing their cement production to support growing infrastructure needs, presenting an opportunity to adopt sustainable practices from the outset. By investing in renewable energy early, these nations can bypass traditional, less eco-friendly methods and position themselves as leaders in green cement production. In India, a recent order mandates that power plants with a capacity of 1 MW or more must source 27.08% of their energy from renewable options, encouraging new cement units to incorporate solar and biomass energy from the start.
Smaller, modular recovery systems are gaining traction as well offering flexibility and scalability in adding renewable energy to cement production. This approach not only cuts costs but also ensures a more dependable and sustainable energy supply for plants over the long term. According to the Department of Energy's Industrial Heat Shot Fact Sheet from September 2022, these packaged modular waste heat recovery units, which range from 0.5 to 2 MW, can significantly reduce installation time and costs, making them an excellent choice for budget-conscious, remote cement facilities.
Cement Waste Heat Recovery System Market Analysis
Cement Waste Heat Recovery System Market Share
The top 4 companies in the cement waste heat recovery system industry are Siemens Energy, MITSUBISHI HEAVY INDUSTRIES, LTD., Thermax Limited, and Kawasaki Heavy Industries Ltd. Together, these firms account for approximately 30% of the market share. They utilize high-efficiency waste heat recovery systems to convert thermal energy from cement kilns into electricity or steam, supporting the energy-intensive nature of cement production while adhering to global environmental regulations and energy efficiency goals.
Siemens Energy, a prominent player in the cement waste heat recovery system market, provides advanced solutions, including Organic Rankine Cycle (ORC)-based systems and high-temperature heat exchangers to capture waste heat from cement kilns. In April 2023, Siemens Energy secured a contract to install a waste heat recovery system at a cement plant in Germany, designed to generate 10 MW of electricity and reduce CO2 emissions by approximately 20,000 tons annually.
Cement Waste Heat Recovery System Market Companies
Some of the key market players operating across the cement waste heat recovery system industry are:
Cement Waste Heat Recovery System Market News
This cement waste heat recovery system market research report includes an in–depth coverage of the industry with estimates & forecast in terms of revenue in ‘USD billion’ from 2021 to 2034, for the following segments:
Click here to Buy Section of this Report
Market, By Application
Market, By Temperature
The above information has been provided for the following regions and countries: