Robotics Welding Market - By Type (Arc Welding, Spot Welding, MIG, TIG, Laser welding), By Payload (<50 kg Payload, 50-150 kg Payload, >150 kg Payload), By Component (Hardware, Software, Services), By End Use, Forecast, 2023 – 2032
Report ID: GMI6977
|
Published Date: October 2023
|
Report Format: PDF
Download Free PDF
Buy Now
$4,123 $4,850
15% off
$4,840 $6,050
20% off
$5,845 $8,350
30% off
Buy now
Premium Report Details
Base Year: 2022
Companies covered: 12
Tables & Figures: 355
Countries covered: 20
Pages: 200
Download Free PDF
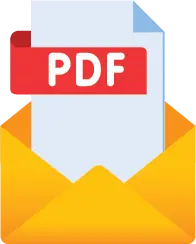
Robotics Welding Market
Get a free sample of this reportGet a free sample of this report Robotics Welding Market
Is your requirement urgent? Please give us your business email for a speedy delivery!
Robotics Welding Market Size
Robotics Welding Market size was valued at USD 7.8 Billion in 2022 and is estimated to register a CAGR of over 10% between 2023 and 2032. The intensification of industry 4.0 principles is driving the market growth due to the rising emphasis on automation, connectivity, and data-driven decision-making.
Industry 4.0 promotes the integration of advanced robotics with real-time data analytics, resulting in more efficient & precise welding processes. The robots equipped with sensors and AI can adapt to the changing conditions, enhance productivity, reduce errors, and ensure consistent quality. This aligns with the requirements of modern manufacturing needs, where efficiency, flexibility, and cost-effectiveness are of the utmost importance. Consequently, the adoption of Industry 4.0 principles acts a catalyst for the increased deployment of robotics solutions in welding applications, propelling market trends.
Robotics welding refers to the use of automated robotic systems to perform welding tasks in various industries. It involves the utilization of robotic arms or devices equipped with welding tools, sensors, as well as Artificial Intelligence (AI) and machine vision technologies. Robotics welding offers several advantages including increased precision, repeatability, and speed as compared to manual welding processes. It is commonly used in the manufacturing, automotive, aerospace, and construction sectors to weld components such as metal parts, pipes, and structural elements. This technology enhances efficiency, reduces labor costs, and ensures consistent weld quality, making it a crucial component of modern industrial automation.
The perceived notion of losing jobs due to automation presents a significant pitfall for the robotics welding market. Many industries are cautious about adopting robotic welding systems due to the fear of displacing human workers. This apprehension can lead to resistance in implementing automation solutions, slowing down market trends. Automation in welding can enhance efficiency, reduce errors, and improve safety. To overcome this pitfall, industry stakeholders should focus on retraining and upskilling the workforce to operate and maintain these robotic systems, highlighting the potential for job augmentation rather than job loss. This shift in perception is essential for realizing the full potential of the market.
COVID-19 Impact
Lockdowns and disruptions in the manufacturing sector led to project delays and reduced investments in automation initiatives. Companies deferred capital expenditures including investments in robotics welding systems to conserve cash. Supply chain interruptions hindered the availability of essential components, further impeding production. Travel restrictions also limited the deployment & maintenance of robotics welding systems, leading to delays and operational challenges for end users. Uncertainties in the market and a cautious approach to investments during the pandemic negatively affected the growth prospects of the robotics welding industry. Overall, the COVID-19 pandemic resulted in decreased demand, disrupted supply chains, and delayed projects, which adversely impacted market expansion.
Robotics Welding Market Trends
The trend of increased automation in the market signifies the growing reliance on robotic systems to perform welding tasks across various industries. This shift is being driven by the need for precision, efficiency, and consistency in welding processes. Robotics welding systems offer advantages such as improved weld quality, reduced labor costs, and enhanced productivity. As industries seek to meet the high production requirements while maintaining weld integrity, automation will become a prominent solution. This trend reflects the industry's recognition of the value that robotics can bring to welding operations, resulting in an expanding market for robotics welding solutions & services.
IoT integration in the market is a prominent trend due to its transformative impact on welding processes. Real-time data collection & analysis is possible by connecting welding robots to the Internet of Things (IoT). This enables remote monitoring of welding operations, predictive maintenance, and performance optimization. IoT integration enhances operational efficiency, reduces downtime, and ensures higher welding quality through constant data feedback. It also facilitates the incorporation of robotics into smart manufacturing ecosystems, thereby enabling seamless coordination with other automated systems. As industries increasingly adopt the industry 4.0 principles, IoT integration in welding robots will become a crucial trend for achieving greater productivity and competitiveness.
Robotics Welding Market Analysis
Based on type, the market is segmented into arc welding and spot welding, MIG (Metal Inert Gas), TIG (Tungsten Inert Gas), laser welding and others. The spot-welding segment dominated the market in 2022, accounting for a revenue of over USD 2.1 Billion in 2022; this segment is also estimated to register a CAGR of about 12% over the forecast period.
Based on end use, the robotics welding market is segmented into automotive & transportation, metals & machinery, electrical & electronics, as well as aerospace & defense. The automotive & transportation segment held a business share of over 8.4% in 2022 and is estimated to grow over the forecast period.
Asia Pacific led the robotics welding market in 2022, accounting for a significant market share of over 10.5%. The Asia Pacific region is experiencing significant growth in the market due to rapid industrialization, the rising demand for automation solutions, and the need for cost-effective labor alternatives. Manufacturers in the region are increasingly adopting robotics welding solutions to enhance productivity and maintain consistent weld quality. The availability of skilled labor, coupled with the government initiatives promoting automation, is driving market trends. The growing automotive and construction sectors in Asia Pacific are fueling the demand for efficient & precise welding processes, leading to the market growth in the region.
Robotics Welding Market Share
The robotics welding market is highly competitive owing to the presence of key players such as:
Significant investments in R&D to gain technological competitiveness and aggressive business strategies including technological launches as well as collaborations and long-term agreements with clients to capture market share are positively impacting market growth.
Robotics Welding Industry News
The robotics welding market research report includes in-depth coverage of the industry, with estimates & forecast in terms of revenue (USD Billion) from 2018 to 2032, for the following segments:
Click here to Buy Section of this Report
By type, 2018 – 2032
By payload, 2018 – 2032
By component, 2018 – 2032
By end use, 2018 – 2032
The above information is provided for the following regions and countries: